The cone crusher is used as one of the main types of first type crushers in mines or ore processing plants. Cone crushers are determined in terms of size and dimensions, either by the diameter of the gap and mantle, or by how large the inlet opening is. Gyratory crushers can be used for primary or secondary crushing. This crushing action inside the gyratory hydrocon is caused by the closing of the gap between the mantle line, which is movable and mounted on the central vertical spindle, with the concave liners, which are fixed and mounted on the main frame of the crusher. This gap is caused by a centrifugal force in the gyrator spindle to open and close and then spray the central vertical spindle. The vertical spindle is free to rotate around its axis. In a gyratory crusher model, the spindle is suspended with a short shaft, which means that the main shaft is suspended from above and the centrifugal center is mounted on the gear. In fact, the short shaft design has replaced the long shaft design, where its center is installed under the gear.
What is a cone crusher?
One of the most widely used secondary crushers is the cone crusher. The cone crusher performs the crushing operation with the help of two pieces of cone and mantle. Crushing process in cone crusher is done by pressure force. The stones enter the machine through the inlet and are placed between the mantle and the cone, then by applying pressure, their size becomes smaller. The parts of this device are made of manganese steel with molybdenum to be highly resistant to wear.
Characteristics of cone crushers
The gyratory stone crusher is suitable for producing large capacities, for example more than 1500 tons per hour and with relatively large dimensions, i.e. more than 600 mm. The main difference between the gyratory crusher and other cone crushers is in the upper shell of the device or their To shell. In the gyratory crusher, this part of the device is completely different and has a higher height, which makes the entrance opening of the crusher bigger and in addition to the entry of larger stones and a larger input load, the production capacity of gravel and sand also increases.
Application of cone crusher
Cone crushers are capable of crushing all kinds of mineral stones with medium to hard hardness. Among the most important features of cone crusher are low energy consumption, strong body, high efficiency (compared to other crushers) and high reduction ratio (feed size, input compared to product size, output). This stone crusher is most used in construction and mining industries. Cone crushers are generally used as secondary crushers.
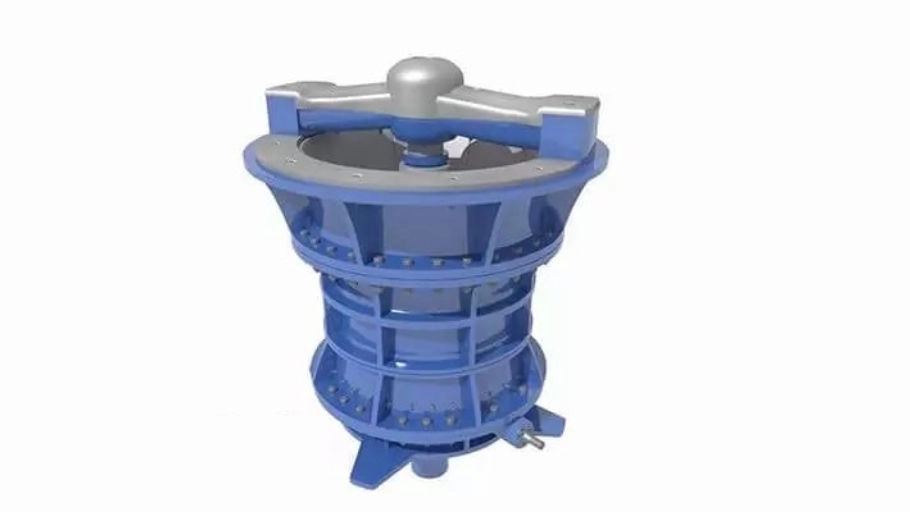
Types of cone crushers
1. Standard cone crusher
2. Short head cone crusher
3. Hydraulic cone crusher
The main parts of cone crushers
Hydrocon parts include various components, each of which plays an important role in the optimal performance of the device. Below is a brief description of each of these parts:
The main shaft of hydrocon: The main shaft is the central axis of the device, where the driving force is transferred from the engine to the crushing cone. This shaft must withstand heavy loads and high compressive force.
Hydrocon small and large paloni: These parts are used to maintain and adjust the distance between the shaft and the main body of the machine. Palloni are designed in different sizes so that the performance of the device is optimal.
Hydrocon spacer: Spacers are used to adjust the distance between different parts of the hydrocon. These distances are necessary for the correct operation of the device and to prevent unnecessary friction and wear.
Round floor of hydrocon lens: This piece is located at the bottom of the crushing cone and has the task of evenly distributing the load and reducing friction. is responsible for The round bottom of the lens improves the crushing performance and increases the useful life of the device.
Hydrocon cranwheel gear: This large gear is used in the Hydrocon power transmission system and transfers the driving force from the engine to the crushing cone. transmits Cranial gear must be resistant to wear and high pressures.
Hydroken cast iron dust collector ring: These rings are used to prevent dust from entering the device. Their cast iron material guarantees high resistance to wear and corrosion.
Hydrocon flat fiber: Flat fiber is used to insulate and reduce machine vibrations. This part plays an important role in maintaining the stability and operation without defects of hydrocon.
Hydrocon pinion gear: The pinion gear is a small gear that is connected to the crankwheel gear and transmits the rotational force to the crushing cone. transmits The pinion gear must be accurate and resistant to pressure.
Hydrocon hydrostatic: Hydrostatic is used to accurately adjust the pressure and flow of oil in the hydraulic system of the machine. These adjustments are necessary for optimal performance and reduced wear of parts.
Hydrocone Mantle: The mantle is the upper part of the crushing cone that presses the minerals against the cone. This part must have high resistance against wear and pressure.
Hydrocon Concave: Concave is the fixed part of the crushing cone against which minerals are crushed. This part should also have high resistance to wear.
Hydrocon head center: The head center is the center of the crushing cone, which distributes the compressive force uniformly. This part plays a key role in the uniform operation of the machine. This part helps to improve the efficiency and useful life of the device.
Hydrocon housing: Housing is a container where different parts of the hydrocon are placed. This chamber must be strong and stable so that all parts work properly. Hydrocon piston: The piston is used in the hydraulic system of the machine to adjust the pressure and movement of the crushing cone. This part must have high precision and good resistance.
Hydrocon spider cup: Spider cup is used to connect and maintain different parts in the central axis. This part plays an important role in the strength and stability of the machine.
Hydrocon steel round bottom: Steel round bottom is used to reduce friction and wear at the contact points of the crushing cone with the body of the machine. This part must be resistant to wear and corrosion. Hydrocon Congress Bush: Congress Bush is used to maintain and guide the main shaft in its axis. This part must have high precision and good resistance.
Hydrocon steel bush: Steel bush is used to reduce friction and increase the useful life of the shaft and various axes of the machine. These bushings should have a high resistance to wear.
Short and long spider bushing: Spider bushings are used to maintain and guide different axes in the machine. These parts are designed in different sizes for specific applications.